Discover What is Porosity in Welding and Its Result on Architectural Honesty
Discover What is Porosity in Welding and Its Result on Architectural Honesty
Blog Article
The Science Behind Porosity: A Comprehensive Guide for Welders and Fabricators
Understanding the detailed systems behind porosity in welding is important for welders and producers making every effort for remarkable workmanship. From the composition of the base materials to the ins and outs of the welding process itself, a wide range of variables conspire to either intensify or reduce the presence of porosity.
Recognizing Porosity in Welding
FIRST SENTENCE:
Evaluation of porosity in welding reveals vital understandings into the integrity and top quality of the weld joint. Porosity, defined by the visibility of cavities or voids within the weld steel, is a typical problem in welding processes. These voids, if not effectively attended to, can endanger the architectural honesty and mechanical homes of the weld, resulting in potential failings in the ended up item.
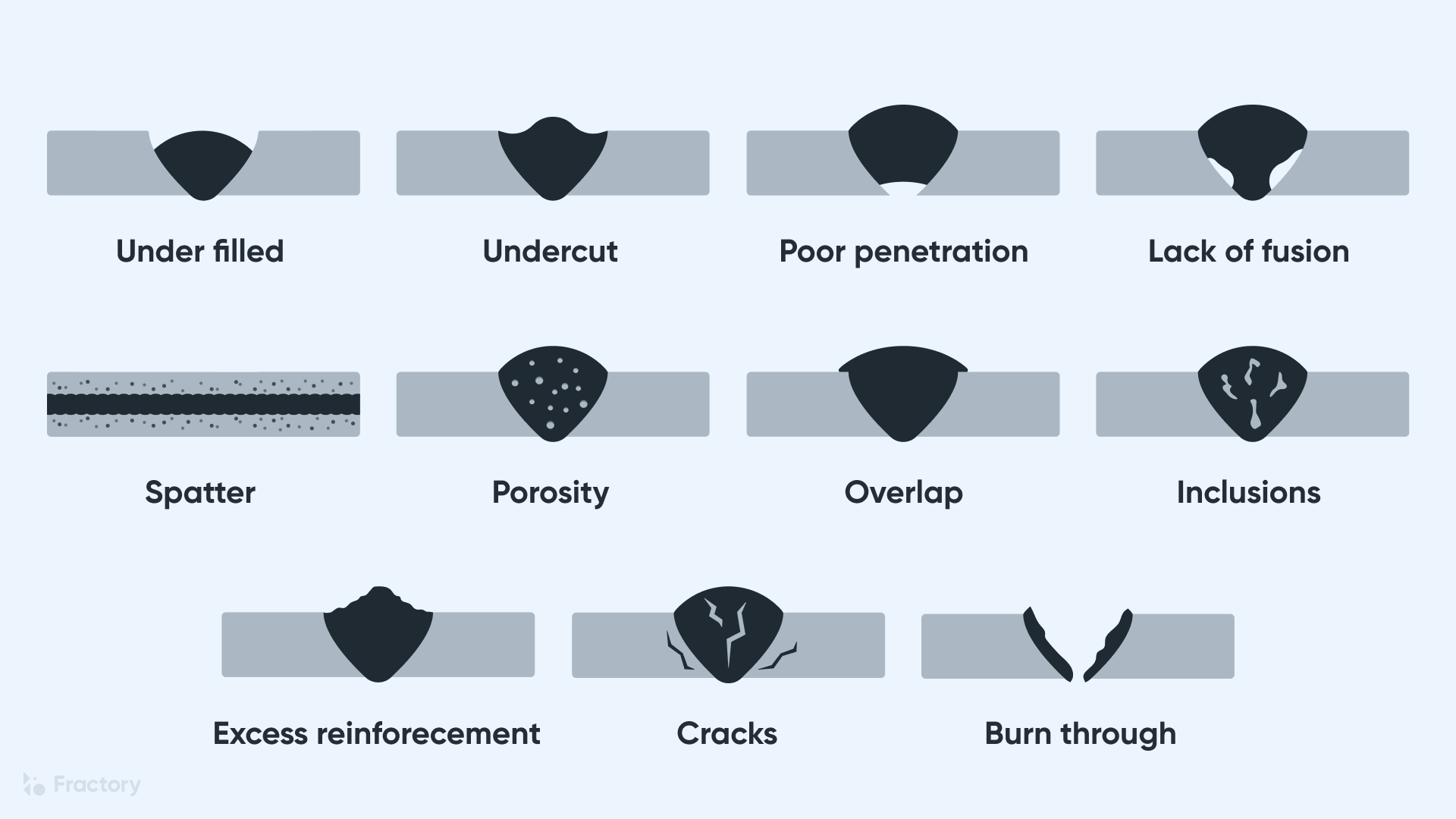
To identify and evaluate porosity, non-destructive testing techniques such as ultrasonic testing or X-ray evaluation are typically employed. These techniques permit the identification of inner problems without endangering the stability of the weld. By analyzing the dimension, form, and distribution of porosity within a weld, welders can make enlightened choices to enhance their welding processes and accomplish sounder weld joints.
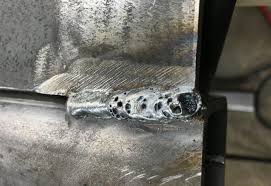
Variables Affecting Porosity Formation
The event of porosity in welding is influenced by a myriad of factors, ranging from gas securing performance to the ins and outs of welding criterion settings. Welding criteria, including voltage, existing, travel speed, and electrode type, also impact porosity development. The welding strategy utilized, such as gas steel arc welding (GMAW) or shielded metal arc welding (SMAW), can affect porosity formation due to variants in warmth circulation and gas protection - What is Porosity.
Effects of Porosity on Weld Quality
The visibility of porosity likewise damages the weld's check here resistance to deterioration, as the entraped air or gases within the spaces can respond with the surrounding environment, leading to deterioration over time. Additionally, porosity can prevent the weld's capacity to stand up to pressure or influence, additional jeopardizing the overall quality and integrity of the bonded structure. In vital applications such as aerospace, automobile, or architectural constructions, where security and longevity are vital, the detrimental impacts of porosity on weld top quality can have extreme effects, highlighting the importance of reducing porosity via proper welding strategies and procedures.
Methods to Minimize Porosity
To boost the high quality of welded joints and make sure architectural stability, welders and producers employ details strategies targeted at lowering the development of spaces and dental caries within the material throughout the welding procedure. One efficient approach to minimize porosity is to make sure proper product prep work. This includes detailed cleansing of the base steel to remove any type of contaminants such as oil, oil, or dampness that could contribute to porosity formation. In addition, using the proper welding criteria, such as the proper voltage, existing, and travel speed, you could try these out is important in stopping porosity. Keeping a consistent arc size and angle throughout welding also helps in reducing the chance of porosity.

Making use of the appropriate welding strategy, such as back-stepping or using a weaving motion, can also help disperse warmth evenly and reduce the opportunities of porosity development. By applying these strategies, welders can properly lessen porosity and produce top notch bonded joints.

Advanced Solutions for Porosity Control
Applying advanced modern technologies and innovative techniques plays an essential duty in achieving remarkable control over porosity in welding procedures. Furthermore, utilizing sophisticated welding methods such as pulsed MIG welding or modified atmosphere welding can likewise help alleviate porosity issues.
Another innovative remedy involves using sophisticated welding tools. As an example, utilizing tools recommended you read with built-in functions like waveform control and advanced power resources can improve weld quality and lower porosity risks. The application of automated welding systems with accurate control over criteria can dramatically lessen porosity defects.
In addition, including sophisticated tracking and examination innovations such as real-time X-ray imaging or automated ultrasonic testing can help in detecting porosity early in the welding process, enabling prompt restorative actions. In general, integrating these sophisticated solutions can substantially improve porosity control and enhance the general top quality of welded components.
Final Thought
Finally, comprehending the science behind porosity in welding is vital for welders and fabricators to produce premium welds. By recognizing the factors influencing porosity formation and applying methods to decrease it, welders can enhance the total weld high quality. Advanced options for porosity control can further boost the welding process and make certain a strong and dependable weld. It is necessary for welders to continually educate themselves on porosity and execute finest techniques to accomplish ideal results.
Report this page